Capacity planning refers to the strategic coordination of available resources and productive hours at company level, while resource planning involves the detailed allocation of tasks and working hours at individual employee level.
Capacity planning
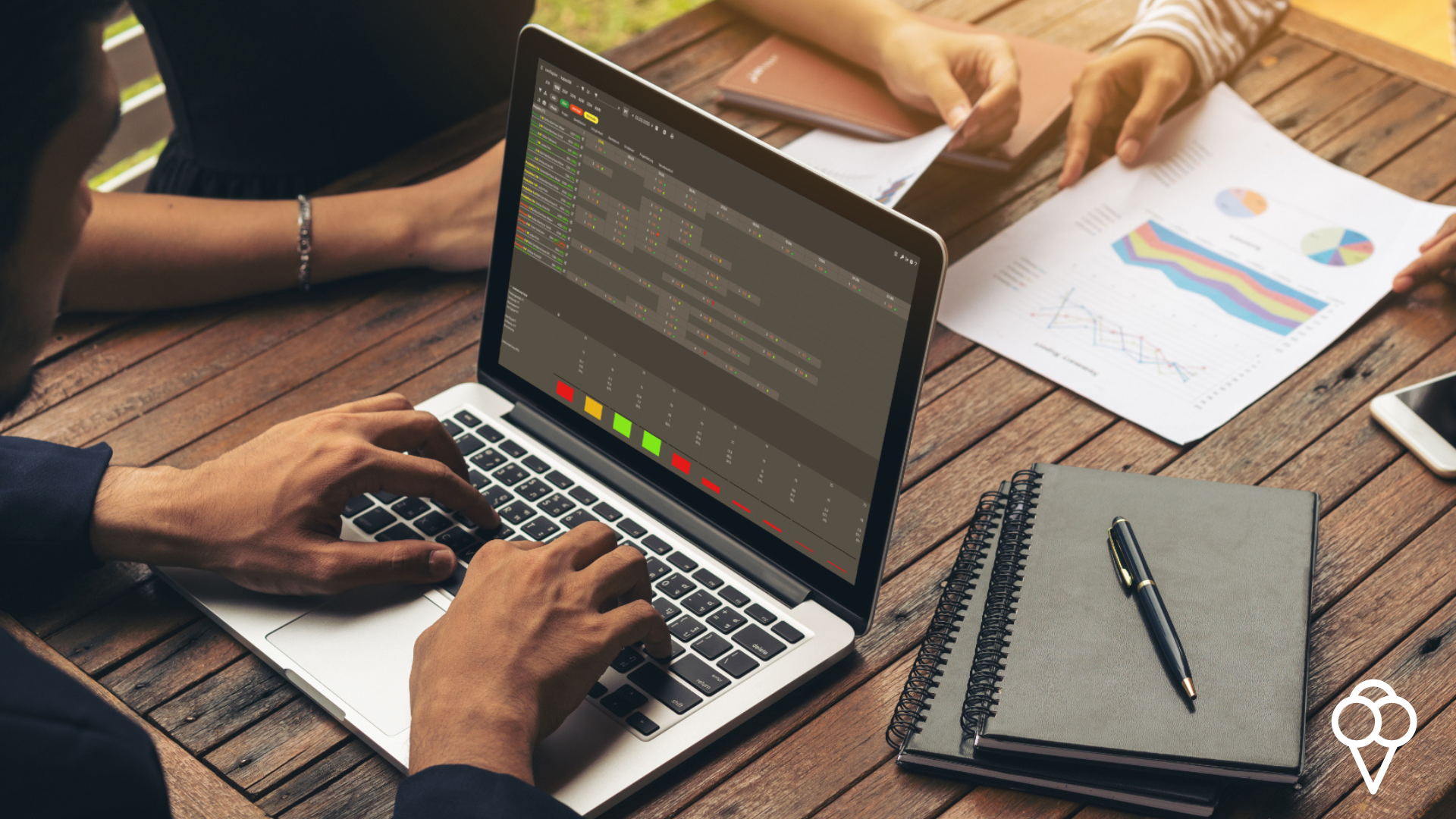
Capacity planning is a central aspect of resource management that takes place at company or department level. In contrast to detailed planning at employee level, which deals with individual working hours and tasks, capacity planning focuses on the overarching coordination of personnel resources and productive hours over a longer period of time. It aims to ensure a balanced utilisation of available resources by reconciling personnel requirements with the capacities actually available.
What is capacity planning?
Capacity planning is a strategic process that aims to match available human resources and productive hours with the requirements of different projects, orders or construction sites. This process is often carried out on a weekly basis, comparing planning results over longer periods of time to identify trends and make adjustments. The main objective of capacity planning is to ensure that the available resources are optimally utilised to maximise the efficiency of the business while avoiding over- or under-utilisation.
Overutilisation and underutilisation: definitions
There are two key terms in the context of capacity planning:
Overutilisation
Occurs when the available productive hours are less than the demand created by current projects and orders. This means that the company does not have enough resources to handle all tasks, which can lead to delays and increased workload.
Underutilisation
Occurs when the available productive hours exceed the requirements. In this case, resources remain unutilised, which leads to inefficiency and can affect the company's productivity.
Measures in the event of overload
When an overload occurs, companies must act quickly to alleviate it. Possible measures include
Using temporary staff: temporary staff can be brought in at short notice to cope with the increased workload without making long-term commitments.
Increasing working hours: In some cases, existing employees can work additional hours to meet the demand.
Outsourcing: Certain tasks can be subcontracted or subcontracted out to reduce the internal workload.
Process optimisation: By improving workflows and processes (e.g. through lean management), companies can work more efficiently and reduce the workload on employees.
Internal reallocation: Available employees from other departments can be deployed at short notice to support overloaded areas.
Measures in the event of under-utilisation
In the event of an underload, there are also various strategies to bridge this phase:
Redeployment of staff: employees can be deployed in other departments that currently have a higher demand.
Loan of employees: Available employees can be temporarily loaned to friendly companies in order to utilise their capacities sensibly.
Short-time working or holidays: In times of low capacity utilisation, short-time working can be introduced or employees can be encouraged to take holidays to spread the workload.
Internal tasks: Employees can take on work in the warehouse or maintenance tasks during this time that might otherwise be neglected.
Key figures in capacity planning
In order to organise capacity planning effectively, various key figures are required. These key figures provide insights into the company's capacity utilisation and resource requirements and enable well-founded decisions to be made. The most important key figures include
Percentage target utilisation
Weekly overview of available and required productive hours
Difference between available and required resources
Project-related data in capacity planning
Project progress
Percentage target utilisation
Percentage target utilisation is a key performance indicator in capacity planning that shows how efficiently the available personnel resources are being used. Over a longer period of time, it shows how the entire company, an individual department or several departments together are utilised in percentage terms per week.
Weekly overview of personnel resources
A weekly overview of personnel resources is an important tool in capacity planning. It shows how many employees are employed, absent, available or temporarily deployed in a particular week. It also shows a comparison of the productive hours required per week.
Difference between available and required personnel
The difference between available and required personnel is crucial for successful capacity planning. A negative difference indicates that additional employees are required, while a positive difference indicates that resources can be freed up. The difference helps to identify staff shortages or surpluses at an early stage and to act accordingly.
Project-related data in capacity planning
Capacity planning requires a list of all projects with detailed information. This includes the project number, project name, location, start and end dates, the planned project duration and the productive hours required (workload or calculated effort; in hours, days or weeks). It must also be possible to see which construction or planning week the project is currently in. This data helps to accurately calculate the required productive hours for each project and ensure that all requirements are met.
Project progress
Project progress is measured in terms of productive hours used compared to planned requirements. Therefore, the key figures for consumed, planned and available productive hours must be displayed for each project. This information makes it possible to evaluate the performance of the project and make any necessary adjustments to ensure that it remains on schedule.
FAQ
An overload can be counteracted by using temporary employees, process optimisation, internal redistribution of personnel or by outsourcing certain tasks.
In the event of underutilisation, staff redeployment, hiring out employees, introducing short-time working or taking over internal tasks such as maintenance can be a sensible solution.
The most important key figures include the target utilisation percentage, available and required productive hours and the difference between available and required resources. These key figures provide insights into resource utilisation and optimise the company's capacity utilisation.
The target utilisation percentage shows how efficiently the available resources are being used. It helps to recognise over- or under-utilisation at an early stage and to take appropriate measures.