The main task of production planning is to optimise the allocation of productive hours of human resources to ongoing construction projects. This includes the planning of machines, robots and workstations to ensure efficient production.
Production planning
Efficient deployment plans for production in timber construction
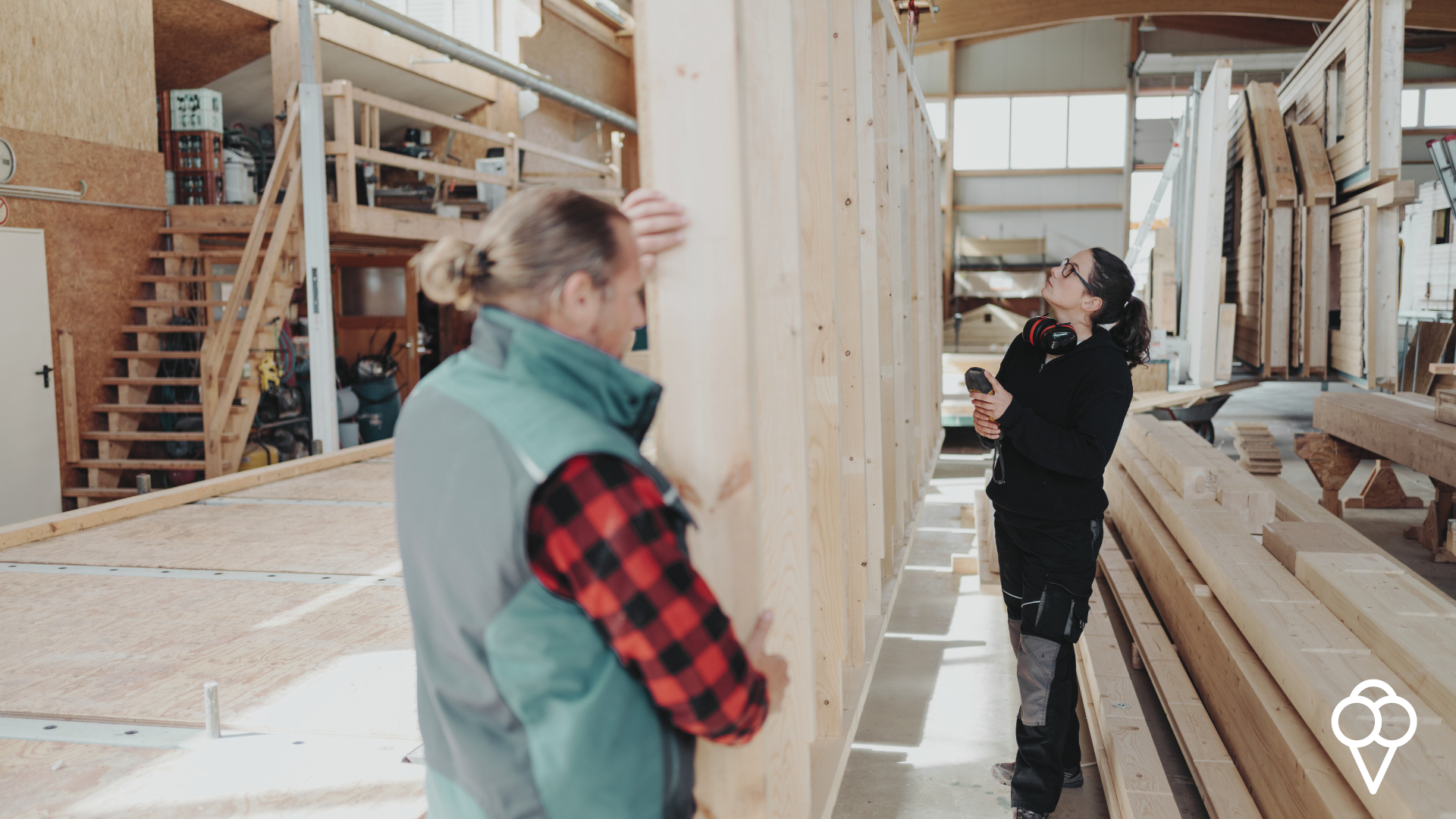
Main task of production planning
In the entry ‘Operational planning’, we saw that the Main task of operational planning is to optimise the distribution of productive hours of personnel resources to ongoing construction projects. In production, for example in timber construction companies that produce timber elements industrially, these basic requirements are the same, but differ in detail.
Requirements for production planning
Shift operation for the planning of machines and robots
When planning the utilisation of machines or robots, machine operators - i.e. personnel - are scheduled to work on them. However, the pace of work is determined by the machines and cannot be accelerated. An increase in efficiency can therefore only be achieved through shift operation (1 to 3 shifts). Therefore, the schedules for production must guarantee shift operation.
Dynamic planning at workstations
At workstations, such as butterfly tables in timber construction, elements are processed by hand. This means that the pace of work can be influenced to a certain extent: The more employees work on it without getting in each other's way, the higher the output. This important requirement must therefore be met by production schedules.
Planning orders on the line
For both machines and workstations, it is essential that orders can be scheduled on the line, as the postponement of an individual project phase requires the machines or workstations to be set up again, which is time-consuming. By scheduling all orders on the line, the entire order can be rescheduled if a project phase is postponed - as can the orders behind it, in order to avoid downtime at work stations.
Short-term rescheduling between workstations
Large orders are processed simultaneously at several workstations. In order to work more efficiently, the same elements, such as ceilings or walls, are produced at each workstation. This means that order packages can be scheduled from one table to another at short notice, depending on capacity utilisation. This flexible rescheduling between workstations must be possible in the schedules.
Overview of all orders in chronological order
To ensure an overview of machines, workstations and projects, all orders must be lined up in a list in chronological order. Orders with delays can thus be pushed forward if possible or accelerated by deploying additional employees.
Procedure for creating production schedules in Vanillaplan
1. Creation of workstations
Firstly, various workstations are created, whereby a distinction is made between machines/robots and workstations for ceilings or walls.
2. Scheduling of the personnel
The next step is to schedule the machines in 1 to 3 shift operation and the workstations with the productive hours of the personnel. Milestones and notes can also be created.
3. Scheduling the orders
In a third step, the orders are allocated to machines and workstations so that as many orders as possible are scheduled on the line. Orders that end too late are highlighted in red and can be moved forward using drag & drop or accelerated by additional personnel.
FAQs
Shift operation is important because the pace of work is dictated by the machines and cannot be accelerated. An increase in efficiency can therefore only be achieved by using several shifts.
At workstations, the pace of work can be influenced to a certain extent by the number of employees. More employees can increase output as long as they do not hinder each other. Work schedules must therefore be dynamic to allow for this adjustment.
Planning orders on the line means that all orders are scheduled so that they can be processed in a fixed order. If a project phase is postponed, the entire order and subsequent orders can be rescheduled to avoid downtime.
Firstly, various workstations are created for machines/robots and ceilings/walls. Personnel are then scheduled for machines and workstations. In a third step, the orders are assigned to machines and workstations. Orders that end too late are highlighted in red and can be moved forward using drag & drop or accelerated by additional personnel.